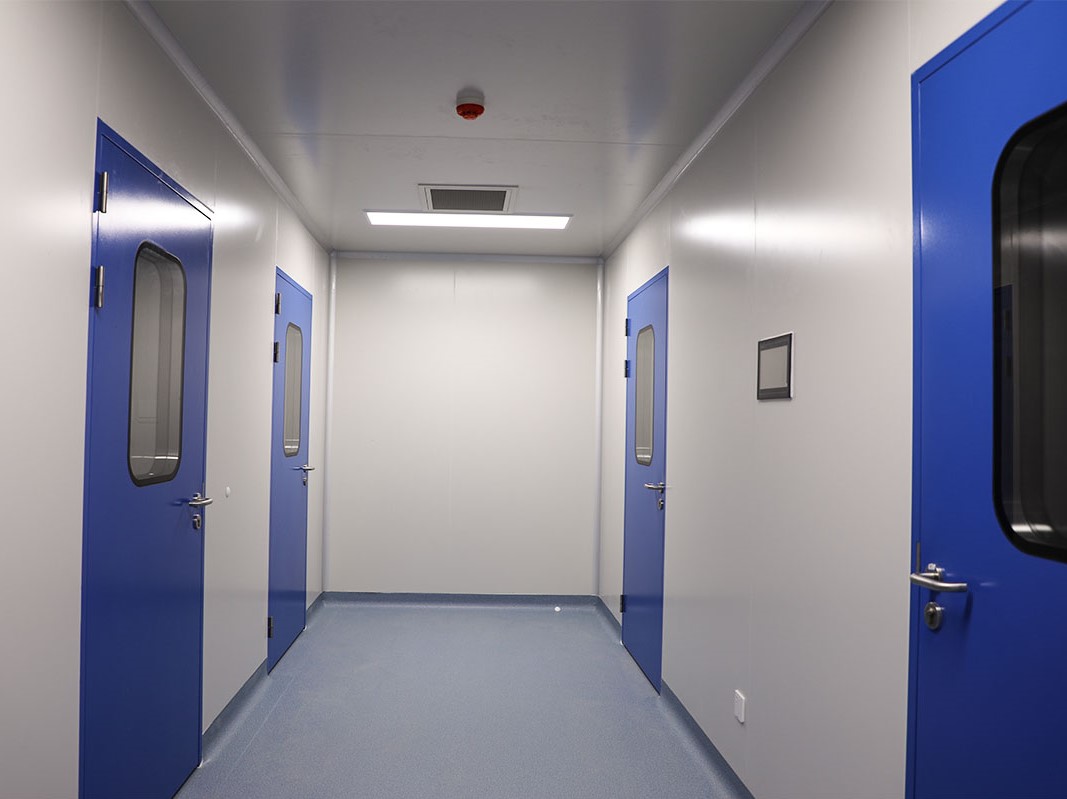
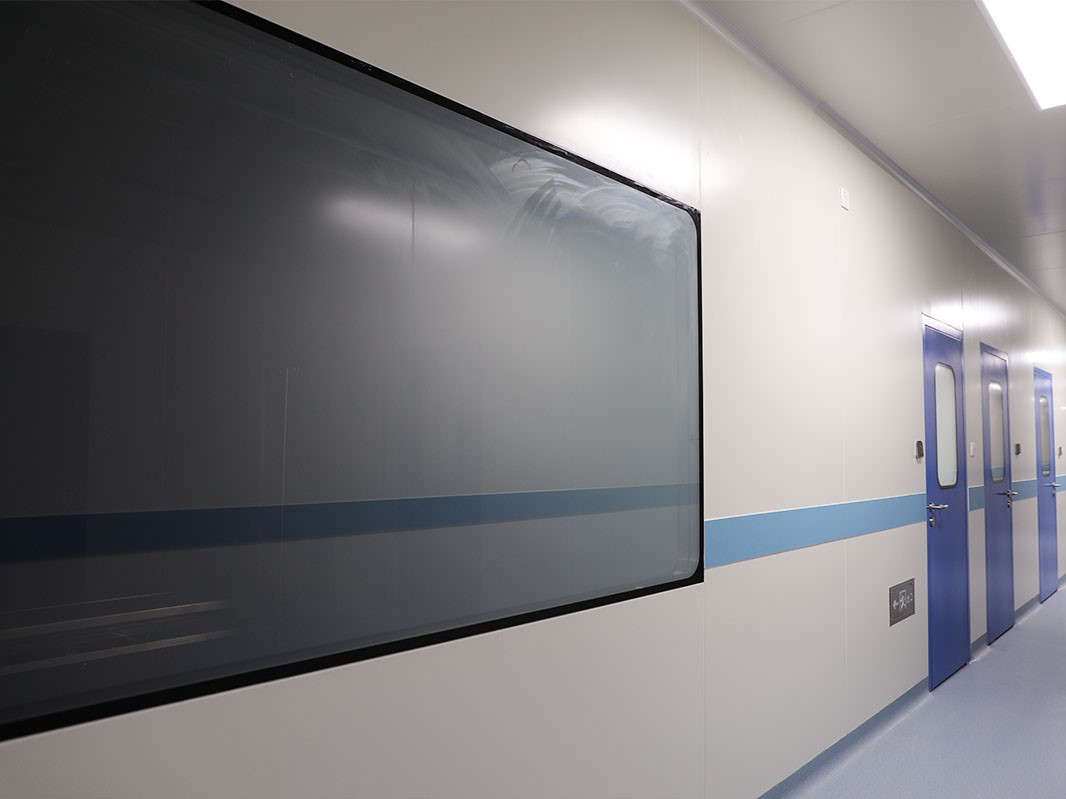
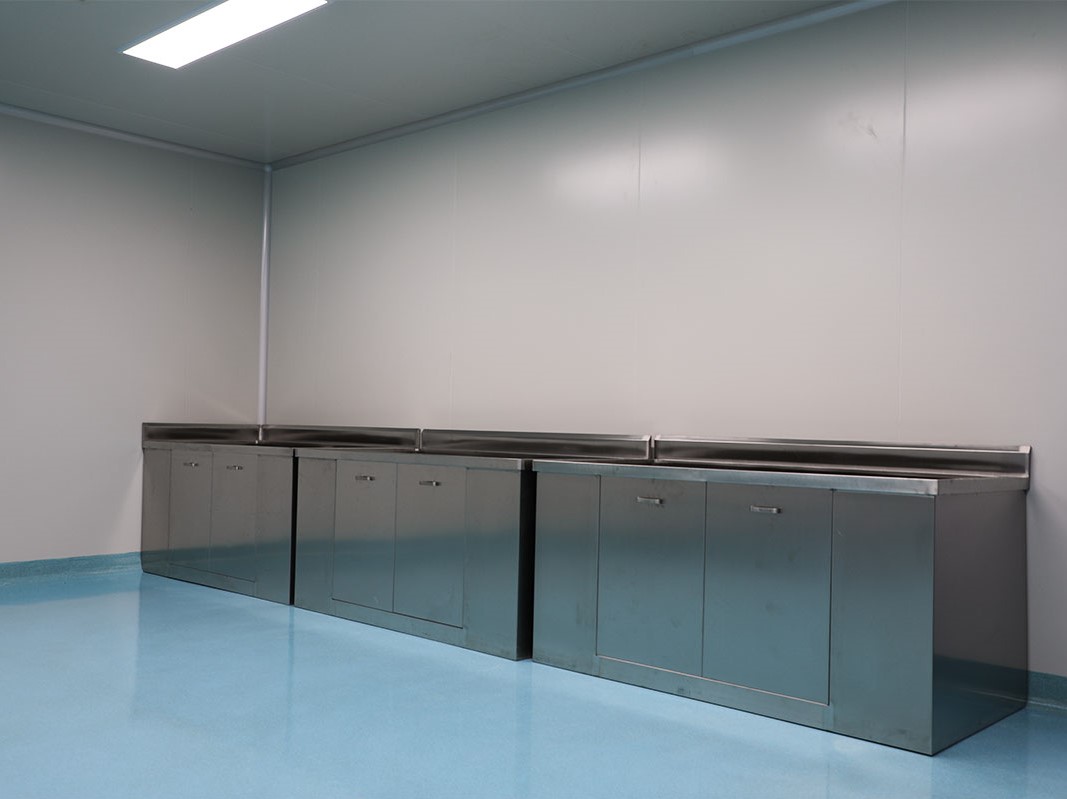
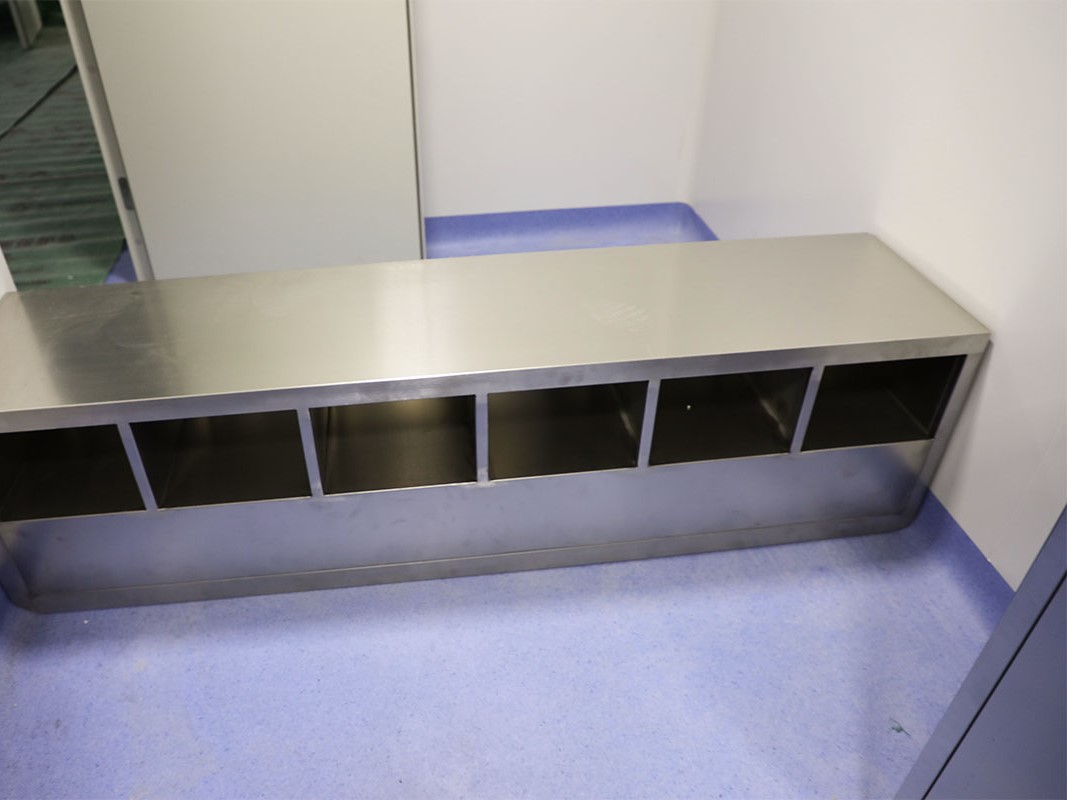
1992 లో ప్రకటించినప్పటి నుండి, చైనా యొక్క ce షధ పరిశ్రమలో "డ్రగ్స్ కోసం మంచి తయారీ అభ్యాసం" (జిఎంపి) క్రమంగా ce షధ ఉత్పత్తి సంస్థలచే గుర్తించబడింది, అంగీకరించబడింది మరియు అమలు చేయబడింది. GMP అనేది సంస్థలకు జాతీయ తప్పనిసరి విధానం, మరియు పేర్కొన్న కాలపరిమితిలో అవసరాలను తీర్చడంలో విఫలమయ్యే సంస్థలు ఉత్పత్తిని నిలిపివేస్తాయి.
GMP ధృవీకరణ యొక్క ప్రధాన కంటెంట్ drug షధ ఉత్పత్తి యొక్క నాణ్యత నిర్వహణ నియంత్రణ. దీని కంటెంట్ను రెండు భాగాలుగా సంగ్రహించవచ్చు: సాఫ్ట్వేర్ నిర్వహణ మరియు హార్డ్వేర్ సౌకర్యాలు. హార్డ్వేర్ సౌకర్యాలలో ప్రధాన పెట్టుబడి భాగాలలో శుభ్రమైన గది భవనం ఒకటి. శుభ్రమైన గది భవనం పూర్తయిన తరువాత, ఇది డిజైన్ లక్ష్యాలను సాధించగలదా మరియు GMP అవసరాలను తీర్చగలదా అనేది చివరికి పరీక్ష ద్వారా ధృవీకరించబడాలి.
శుభ్రమైన గది తనిఖీ సమయంలో, వారిలో కొందరు పరిశుభ్రత తనిఖీలో విఫలమయ్యారు, కొందరు ఫ్యాక్టరీకి స్థానికంగా ఉన్నారు, మరికొన్ని మొత్తం ప్రాజెక్ట్. తనిఖీ అర్హత లేకపోతే, రెండు పార్టీలు సరిదిద్దడం, డీబగ్గింగ్, క్లీనింగ్ మొదలైన వాటి ద్వారా అవసరాలను సాధించినప్పటికీ, ఇది తరచుగా చాలా మానవశక్తి మరియు భౌతిక వనరులను వృధా చేస్తుంది, నిర్మాణ కాలాన్ని ఆలస్యం చేస్తుంది మరియు GMP ధృవీకరణ ప్రక్రియను ఆలస్యం చేస్తుంది. పరీక్షకు ముందు కొన్ని కారణాలు మరియు లోపాలను నివారించవచ్చు. మా వాస్తవ పనిలో, అర్హత లేని పరిశుభ్రత మరియు GMP వైఫల్యానికి ప్రధాన కారణాలు మరియు మెరుగుదల చర్యలు:
1. అసమంజసమైన ఇంజనీరింగ్ డిజైన్
ఈ దృగ్విషయం చాలా అరుదు, ప్రధానంగా తక్కువ శుభ్రత అవసరాలతో చిన్న శుభ్రమైన గదుల నిర్మాణంలో. క్లీన్ రూమ్ ఇంజనీరింగ్లో పోటీ ఇప్పుడు సాపేక్షంగా తీవ్రంగా ఉంది మరియు కొన్ని నిర్మాణ యూనిట్లు ఈ ప్రాజెక్టును పొందటానికి వారి బిడ్లలో తక్కువ కొటేషన్లను అందించాయి. నిర్మాణం యొక్క తరువాతి దశలో, కొన్ని యూనిట్లు మూలలను కత్తిరించడానికి మరియు తక్కువ పవర్ ఎయిర్ కండిషనింగ్ మరియు వెంటిలేషన్ కంప్రెసర్ యూనిట్లను వారి జ్ఞానం లేకపోవడం వల్ల ఉపయోగించారు, దీని ఫలితంగా సరిపోలని సరఫరా శక్తి మరియు శుభ్రమైన ప్రాంతం, ఫలితంగా అర్హత లేని పరిశుభ్రత ఏర్పడింది. మరొక కారణం ఏమిటంటే, డిజైన్ మరియు నిర్మాణ ప్రారంభమైన తర్వాత వినియోగదారు కొత్త అవసరాలు మరియు శుభ్రమైన ప్రాంతాన్ని జోడించారు, ఇది అసలు డిజైన్ను అవసరాలను తీర్చలేకపోతుంది. ఈ పుట్టుకతో వచ్చే లోపం మెరుగుపరచడం కష్టం మరియు ఇంజనీరింగ్ డిజైన్ దశలో నివారించాలి.
2. హై-ఎండ్ ఉత్పత్తులను తక్కువ-ముగింపు ఉత్పత్తులతో భర్తీ చేయడం
శుభ్రమైన గదులలో HEPA ఫిల్టర్ల అనువర్తనంలో, 100000 లేదా అంతకంటే ఎక్కువ పరిశుభ్రత స్థాయితో గాలి శుద్దీకరణ చికిత్స కోసం, ప్రాధమిక, మధ్యస్థ మరియు HEPA ఫిల్టర్ల యొక్క మూడు-స్థాయి వడపోతను ఉపయోగించాలని దేశం నిర్దేశిస్తుంది. ధ్రువీకరణ ప్రక్రియలో, ఒక పెద్ద శుభ్రమైన గది ప్రాజెక్ట్ హెపా ఎయిర్ ఫిల్టర్ను 10000 యొక్క శుభ్రత స్థాయిలో భర్తీ చేయడానికి సబ్ హెపా ఎయిర్ ఫిల్టర్ను ఉపయోగించినట్లు కనుగొనబడింది, దీని ఫలితంగా అర్హత లేని పరిశుభ్రత ఏర్పడింది. చివరగా, GMP ధృవీకరణ యొక్క అవసరాలను తీర్చడానికి అధిక-సామర్థ్య వడపోత భర్తీ చేయబడింది.
3. వాయు సరఫరా వాహిక లేదా వడపోత యొక్క పేలవమైన సీలింగ్
ఈ దృగ్విషయం కఠినమైన నిర్మాణం వల్ల సంభవిస్తుంది, మరియు అంగీకారం సమయంలో, అదే వ్యవస్థలో ఒక నిర్దిష్ట గది లేదా భాగం అర్హత లేదని కనిపిస్తుంది. మెరుగుదల పద్ధతి వాయు సరఫరా వాహిక కోసం లీకేజ్ టెస్ట్ పద్ధతిని ఉపయోగించడం, మరియు వడపోత యొక్క లీకేజ్ స్థానాన్ని గుర్తించడానికి, క్రాస్-సెక్షన్, సీలింగ్ జిగురు మరియు వడపోత యొక్క సంస్థాపనా ఫ్రేమ్ను స్కాన్ చేయడానికి ఫిల్టర్ ఒక కణ కౌంటర్ను ఉపయోగిస్తుంది మరియు దానిని జాగ్రత్తగా మూసివేస్తుంది.
4. రిటర్న్ ఎయిర్ డక్ట్స్ లేదా ఎయిర్ వెంట్స్ పేలవమైన డిజైన్ మరియు ఆరంభం
డిజైన్ కారణాల పరంగా, కొన్నిసార్లు స్థల పరిమితుల కారణంగా, "టాప్ సప్లై సైడ్ రిటర్న్" లేదా తగినంత సంఖ్యలో రిటర్న్ ఎయిర్ వెంట్స్ వాడకం సాధ్యం కాదు. డిజైన్ కారణాలను తొలగించిన తరువాత, రిటర్న్ ఎయిర్ వెంట్స్ యొక్క డీబగ్గింగ్ కూడా ఒక ముఖ్యమైన నిర్మాణ లింక్. డీబగ్గింగ్ మంచిది కాకపోతే, రిటర్న్ ఎయిర్ అవుట్లెట్ యొక్క నిరోధకత చాలా ఎక్కువగా ఉంటుంది మరియు రిటర్న్ ఎయిర్ వాల్యూమ్ సరఫరా గాలి పరిమాణం కంటే తక్కువగా ఉంటుంది, ఇది అర్హత లేని పరిశుభ్రతకు కూడా కారణమవుతుంది. అదనంగా, నిర్మాణ సమయంలో భూమి నుండి రిటర్న్ ఎయిర్ అవుట్లెట్ యొక్క ఎత్తు కూడా పరిశుభ్రతను ప్రభావితం చేస్తుంది.
5. పరీక్ష సమయంలో శుభ్రమైన గది వ్యవస్థకు తగినంత స్వీయ శుద్దీకరణ సమయం
నేషనల్ స్టాండర్డ్ ప్రకారం, శుద్దీకరణ ఎయిర్ కండిషనింగ్ వ్యవస్థ సాధారణంగా పనిచేసే 30 నిమిషాల తర్వాత పరీక్ష ప్రయత్నం ప్రారంభించబడుతుంది. నడుస్తున్న సమయం చాలా తక్కువగా ఉంటే, అది అర్హత లేని శుభ్రతను కూడా కలిగిస్తుంది. ఈ సందర్భంలో, ఎయిర్ కండిషనింగ్ ప్యూరిఫికేషన్ సిస్టమ్ యొక్క ఆపరేటింగ్ సమయాన్ని తగిన విధంగా పొడిగించడం సరిపోతుంది.
6. శుద్దీకరణ ఎయిర్ కండిషనింగ్ వ్యవస్థ పూర్తిగా శుభ్రం చేయబడలేదు
నిర్మాణ ప్రక్రియలో, మొత్తం శుద్దీకరణ ఎయిర్ కండిషనింగ్ వ్యవస్థ, ముఖ్యంగా సరఫరా మరియు తిరిగి గాలి నాళాలు ఒకేసారి పూర్తి కాలేదు, మరియు నిర్మాణ సిబ్బంది మరియు నిర్మాణ వాతావరణం వెంటిలేషన్ నాళాలు మరియు ఫిల్టర్లకు కాలుష్యాన్ని కలిగిస్తుంది. పూర్తిగా శుభ్రం చేయకపోతే, ఇది పరీక్ష ఫలితాలను నేరుగా ప్రభావితం చేస్తుంది. నిర్మించేటప్పుడు శుభ్రం చేయడం మెరుగుదల కొలత, మరియు పైప్లైన్ సంస్థాపన యొక్క మునుపటి విభాగాన్ని పూర్తిగా శుభ్రం చేసిన తరువాత, పర్యావరణ కారకాల వల్ల కలిగే కాలుష్యాన్ని నివారించడానికి ప్లాస్టిక్ ఫిల్మ్ను మూసివేయడానికి ఉపయోగించవచ్చు.
7. శుభ్రమైన వర్క్షాప్ పూర్తిగా శుభ్రం చేయబడలేదు
నిస్సందేహంగా, పరీక్ష కొనసాగడానికి ముందు శుభ్రమైన వర్క్షాప్ను పూర్తిగా శుభ్రం చేయాలి. శుభ్రపరిచే సిబ్బంది యొక్క మానవ శరీరం వల్ల కలిగే కాలుష్యాన్ని తొలగించడానికి శుభ్రపరచడం కోసం శుభ్రమైన పని బట్టలు ధరించడానికి తుది తుడిచిపెట్టే సిబ్బంది అవసరం. శుభ్రపరిచే ఏజెంట్లు పంపు నీరు, స్వచ్ఛమైన నీరు, సేంద్రీయ ద్రావకాలు, తటస్థ డిటర్జెంట్లు మొదలైనవి కావచ్చు. యాంటీ స్టాటిక్ అవసరాలు ఉన్నవారికి, యాంటీ-స్టాటిక్ ద్రవంలో ముంచిన వస్త్రంతో పూర్తిగా తుడిచివేయండి.
పోస్ట్ సమయం: జూలై -26-2023